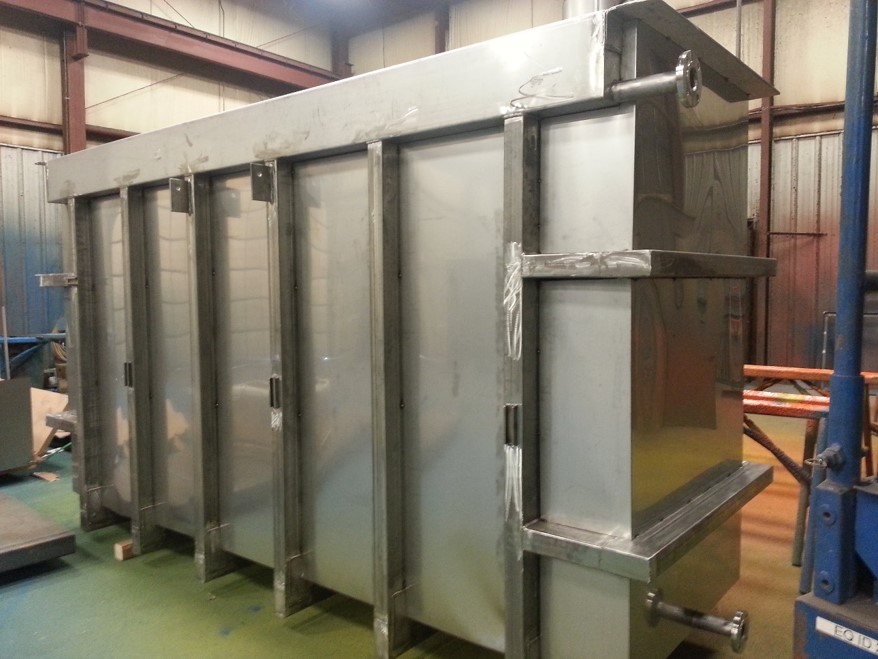
From playing and rinsing to storage, tanks are used in nearly every step of the surface finishing process. Selecting the right tank for each stage of your process contributes to the long-term success of your entire operation. Seacole is here to help you decide which tanks are right for your surface finishing line.
Chemical, Temperature, and Electrical Insulation Considerations for Surface Finishing Tanks
Each step in your surface finishing process requires a different chemistry, temperature tolerance, and insulation against electrical currents. Some tanks are designed for acidic processes, while others are developed for alkaline chemistries. Tanks with high chemical resistance are required for corrosive processes.
If your surface finishing process involves chemical reactions that produce heat or electrical currents, your tanks will need to be able to hand those stresses. Consider both the temperature of your process and the need for electrical insulation when selecting tanks for your surface finishing process.
Plastic Tanks for Surface Finishing
Most plastic tanks are excellent temperature and electrical insulators, making them ideal for high-temperature processes or electroplating. The most common materials for plastic surface finishing tanks are polypropylene, PVC, polyethylene, and Kynar®.
- Polypropylene: The most common tank material for metal finishing due to its low cost, chemical resistance, and appearance. Use for rinse water or with acidic or alkaline materials. Do not use for nitric or chrome processes.
- PVC: Most common tank for chrome processes. Has a shorter lifespan.
- Polyethylene: Ideal for molded, round storage tanks.
- Kynar®: A greater investment but offers excellent chemical resistance. Ideal for high temperatures. Do not use for highly alkaline materials.
Steel Tanks for Surface Finishing
There are several different types of steel tanks for surface finishing. All steel tanks must be lined for electrical insulation if used in plating. The most common types of steel tanks are mild steel and stainless.
- Mild steel: Low-cost, but suitable only for alkaline chemistries. Most mild steel tanks are coated with epoxy on the outside for durability.
- 304 stainless steel: An affordable option for stainless steel and ideal for most chemistries except fluorides and chromic acid. Must be lined for electrical insulation if used as a plating tank.
- 316 stainless steel: Often used for applications involving high-temperature pure water. Like 304 stainless steel, 316 stainless shouldn’t be used with fluorides or chromic acid. Must be lined for electrical insulation if used as a plating tank.
Lined Tanks for Surface Finishing
Lined tanks are tanks lined with PVC, Kynar®, or Teflon®. In some lined tanks, the liner is bonded to the tank walls. Other times, a bag or rigid liner can be retrofitted into an existing tank to insulate it against electric current or fix a leak. PVC is the most common liner material for plating tanks, though it is not ideal for temperatures over 150 degrees Fahrenheit. Kynar® and Teflon® are ideal for high temperatures and processes involving chrome and fluorides.
Don’t Overlook Ventilation
Ventilation is another key consideration in choosing the right tank for your surface finishing process. To keep employees safe and your surface finishing line productive and efficient, you must properly ventilate your process tanks. The design of your process’s ventilation hood, ductwork, and scrubbers must ensure that hazardous fumes are safely scrubbed and ventilated out of your facility.
Choosing the right tanks for your surface finishing process can be complicated, so rely on the expertise of the Seacole surface finishing team to help you identify the best tanks for every step in your process. Contact the Seacole team today.